The Secret to Flying High: Building Our Batteries In-House
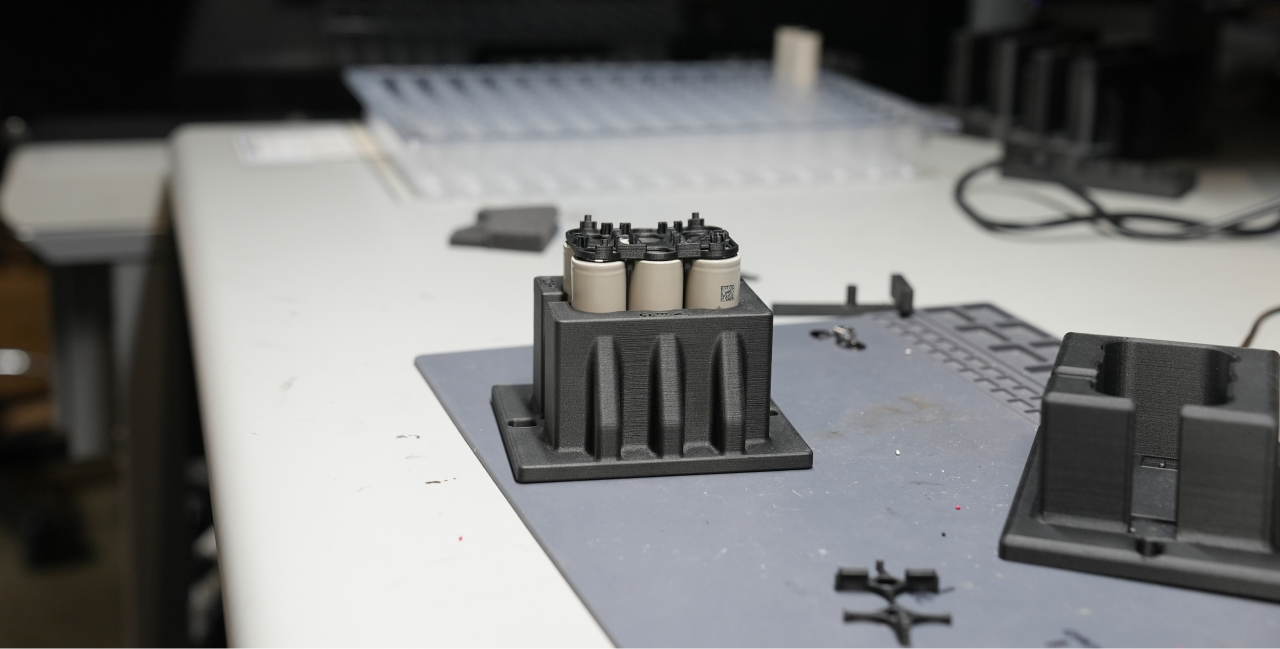
Critical components require critical attention.
There’s a good case to be made that the battery – the oft-overlooked, lowly battery – should be considered the most important part of a drone.
Autonomy is cool. Communication is critical. But the battery is essential.
That’s why at BRINC, we build our batteries from scratch. The BMS circuit board is BRINC-designed and uses U.S.-sourced chips. The injection molded plastic enclosure is developed in house and manufactured by trusted suppliers. We even do the battery welding in our Seattle joint R&D and manufacturing facility.
This allows us to continue making and delivering drones at the same rate despite concerted Chinese efforts to sanction US drone companies.
Batteries are what keep BRINC and our agencies airborne, so we’ve put in the effort to become masters at building them.
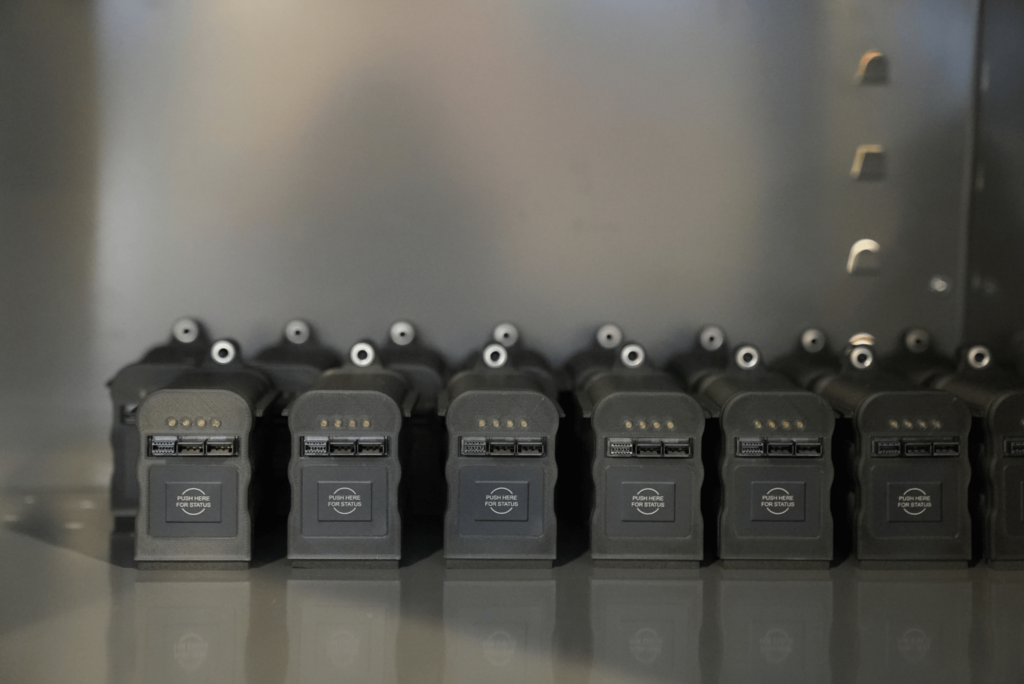
Building a Better Battery
At BRINC, we procure top-quality components from manufacturers in trusted U.S.-allied nations while maintaining the flexibility to assemble and customize the batteries in our Seattle headquarters.
This lets us source the leading-edge battery cells and move them into production. In fact, the battery cells we’re shipping today in our Lemur 2 and Responder airframes are the same battery cells that power the McMurtry Spéirling PURE Validation Prototype high-performance electric sports car.
By building our batteries in-house, we can control every aspect of the design and tailor it to meet public safety demands. That means we’re constantly working on not only creating the lightest battery possible—reducing any unnecessary bulk—but also ensuring each part of our batteries are as visually consistent as they are functional.
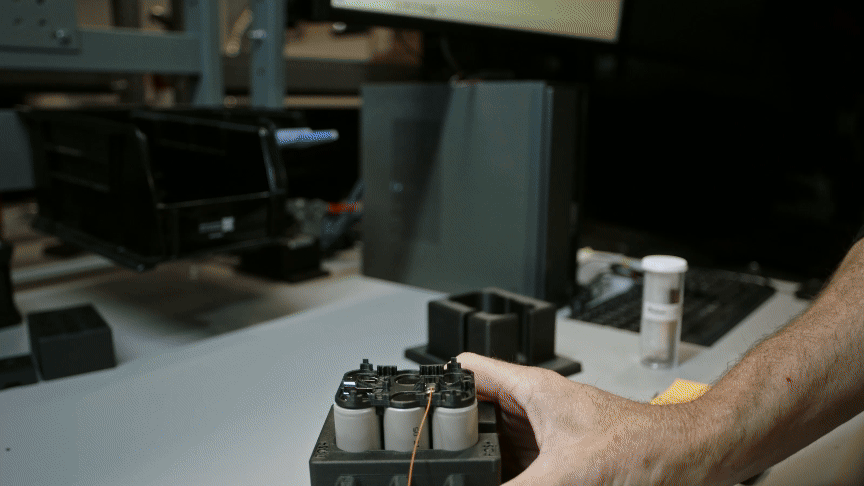
Consistency Is King
Building our own batteries lets us learn from previous generations to make better batteries today. Both our Lemur 2 and Responder drones share the same battery cells and battery management system (BMS), just a different amount of cells and unique mounting mechanisms. This allows batteries for both airframes to maintain the same charging adapters and USB-C charging method across the board, giving operators the freedom to interchange accessories. Additionally, by using USB-C for charging, lost cables can be replaced easily.
Assembling in-house also lets us take two different approaches to mounting batteries on our drones. With Lemur 2, where the airframe goes inside buildings and often takes a beating, we’ve used thumb screws, which have an incredibly tough fit. For Responder, we’ve switched to a squeeze-and-release mechanism for faster battery swapping while keeping a firm fit.
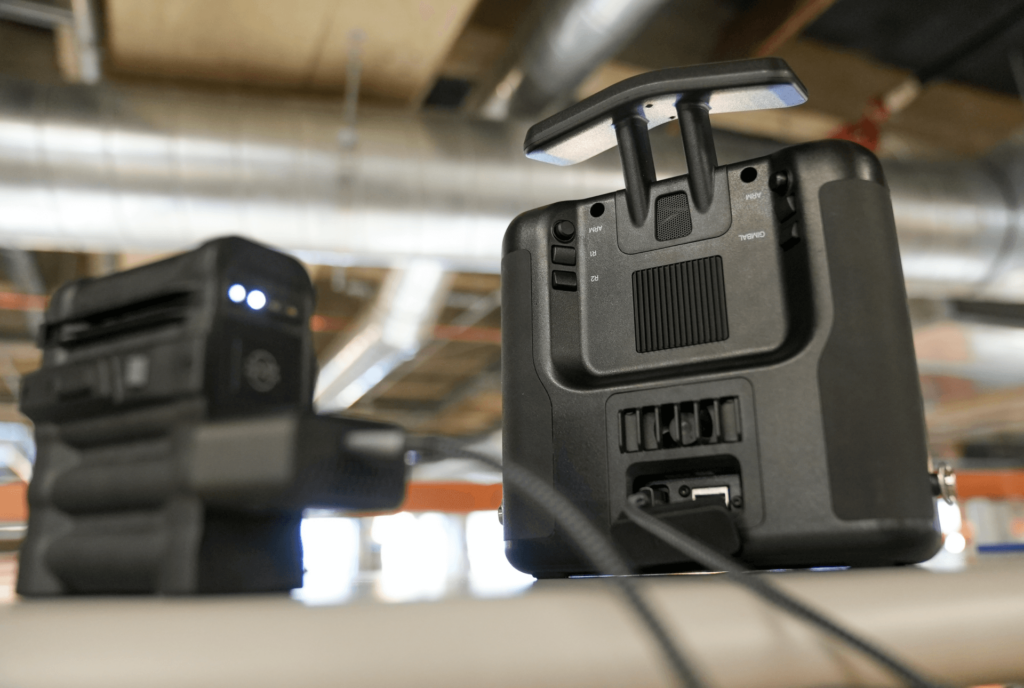
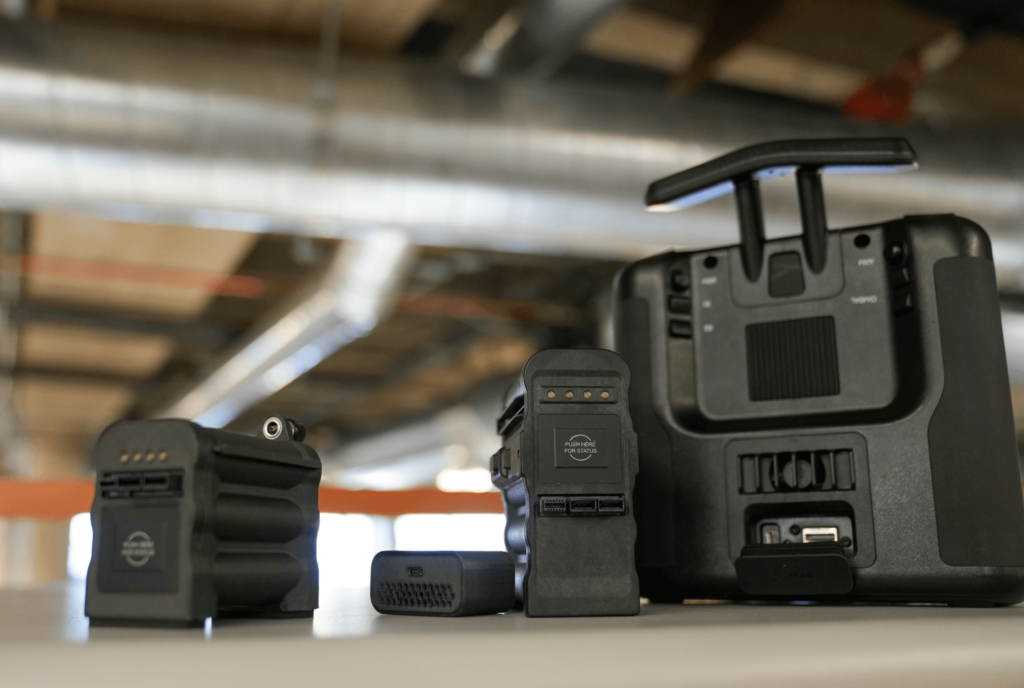
Adjustments on the Fly
Another advantage of building our batteries in-house is that we can iterate quickly, which is essential in a field where small changes can significantly improve performance.
Other companies that work with a contract manufacturer use a battery designed once and never touched again. As a result, they can often lag a year or two behind in battery chemistry, which means we are often a few percentage points better in flight time (which equals real operational minutes) than those frozen in the past.
But let’s say we want to develop a new product, we don’t have to contact an outside company to tweak the battery settings. We are able to quickly modify what we have in-house to meet the requirements of the new design.
With each battery, we’re advancing our technology, staying on the cutting-edge of innovation, and supporting the dedicated public safety professionals who rely on it.
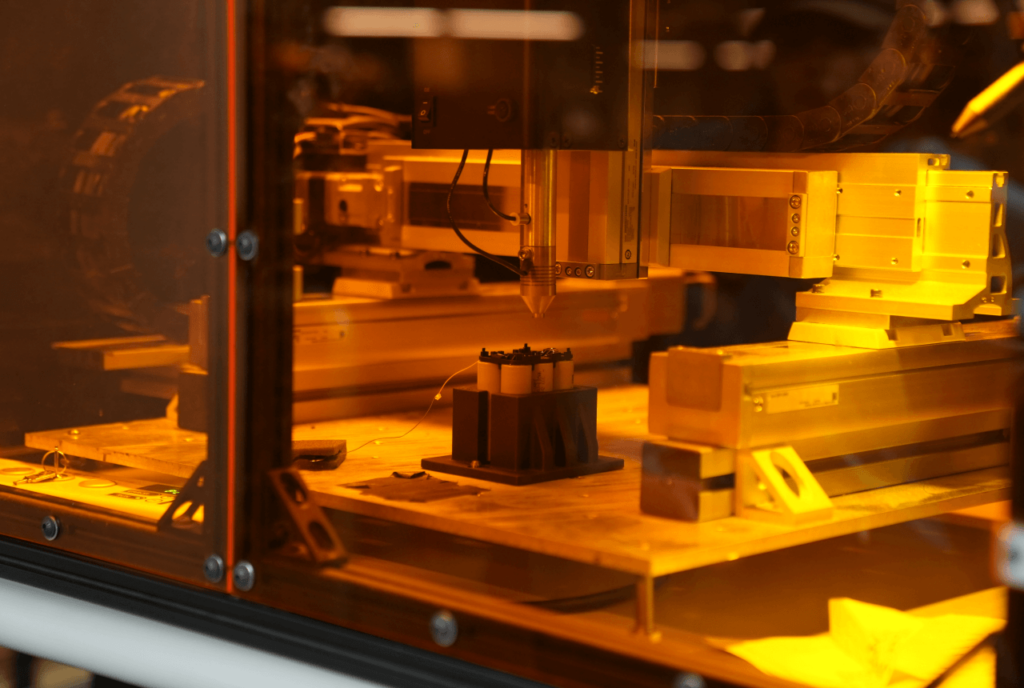
Testing Is the Best Thing
We know public safety agencies, and the communities they serve, rely on our drones. That’s a big responsibility. So BRINC goes beyond regulatory certification when it comes to our batteries. Not only are they 3rd-party lab tested to achieve UN 38.3 certification, our batteries also undergo rigorous in-house testing to ensure they’re ready for real-world conditions.
We use a parachute shock simulator to ensure our batteries can handle worst-case physical loads.
For environmental testing, we verify battery performance in varied conditions (both extreme heat and cold) as part of the full drone.
And we perform rigorous cycle testing to ensure our batteries don’t unnecessarily decay over time. After 500 cycles, our batteries retain most of their original capacity, maintaining high efficiency and longevity.
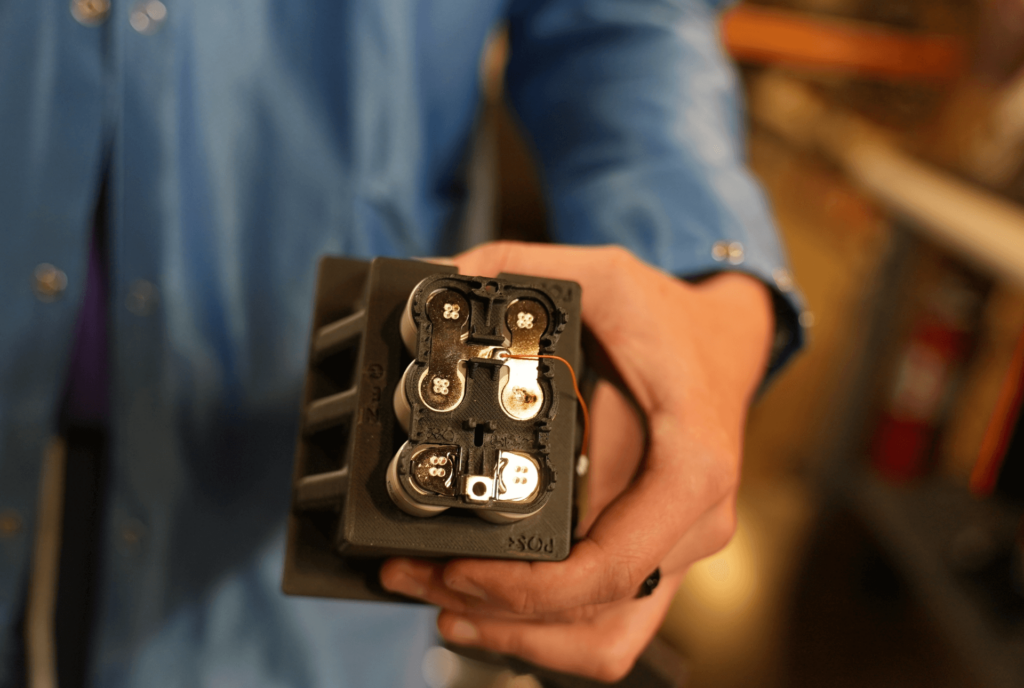
Here’s to the Future
Ultimately, better flight times for public safety drones will come down to better batteries.
By staying on the forefront of battery innovation, BRINC is well-positioned to power our drones well into the future, keeping public safety agencies well-equipped and communities safe.
If your agency would like to learn more about BRINC drones and how they can support your agency, reach out to us here.